This post is an external link. Please follow this link:
Introduction
Cyber-Physical Systems (CPS) are the integration of computing, networking, and physical components to create a smarter, more adaptive system. In simpler terms, it is the convergence of the digital and physical worlds to enable real-time data exchange and decision-making. In the context of manufacturing, CPS has been instrumental in driving digital transformations which lead companies into Industry 4.0.
The Anatomy of Cyber-Physical Systems
Computing Components
- Embedded computers: These miniature devices are integrated with other components to manage data and execute control functions.
- Cloud resources: Cloud-based tools and platforms provide scalable storage and computing capabilities.
- Big data analytics: Advanced data analytics tools facilitate real-time insights and decision-making.
Networking Components
- Wireless communication: Wireless communication technologies are essential for establishing connectivity and data exchange between various components of a CPS.
- Internet of Things (IoT): IoT devices, such as sensors and actuators, collect and transmit data to facilitate communication and interaction.
Physical Components
- Robots and autonomous vehicles: These devices perform a variety of tasks, such as assembly, material handling, and transport.
- Smart factories: Factories are equipped with advanced sensors and systems for monitoring, controlling, and optimising production processes.
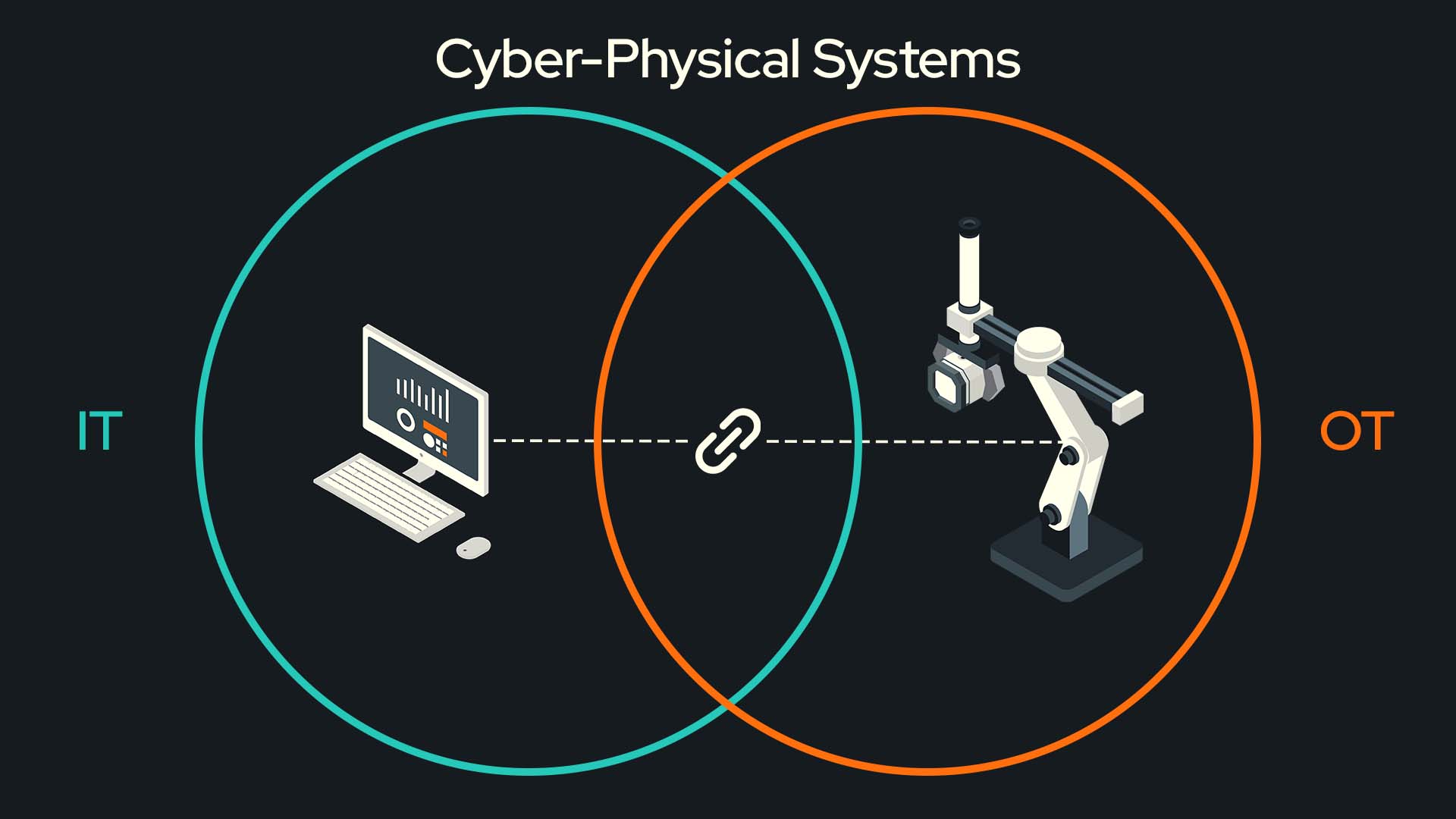
Impact of CPS on Manufacturing
Enhanced Productivity
CPS can lead to significant improvements in productivity, as the increased automation and real-time data exchange enable better resource allocation and process optimisation. The continuous flow of data helps manufacturers to identify bottlenecks, improve production quality, and reduce downtime.
Greater Flexibility
CPS can offer greater flexibility in production processes by allowing real-time adjustments based on changing conditions, such as fluctuations in demand, component availability, or equipment status. This agility can lead to cost savings, as it enables manufacturers to adapt their operations quickly and efficiently.
Improved Safety and Reliability
By incorporating advanced sensors and monitoring systems, CPS can enhance safety and reliability in manufacturing environments. For example, the system can detect potential hazards, such as equipment malfunctions or code compliance issues, and take corrective action to prevent accidents and ensure operational stability.
Reduced Environmental Impact
Another significant benefit of deploying CPS in manufacturing is the reduction in environmental impact. By optimising processes and minimising waste, CPS can contribute to more sustainable production and lower emissions.
Facilitating Customisation
CPS can facilitate the production of customised products on a large scale, thanks to its ability to adapt quickly to changes in demand and specifications. This dynamic flexibility enables manufacturers to deliver tailored products to their customers without sacrificing efficiency or quality.
CPS in the Automotive Industry
An example of cyber-physical systems in the automotive industry is with the use of autonomous robots in the production process.
OEMs use autonomous robots to assist with various tasks, such as welding, painting, and assembly. These robots are equipped with sensors, cameras, and other technologies that enable them to navigate the factory floor, communicate with other machines, and perform their tasks with a high degree of precision and accuracy.
In addition to improving efficiency and reducing costs, the use of autonomous robots also improves safety in the factory. By automating dangerous or repetitive tasks, workers are less likely to be injured on the job.
Overall, the use of cyber-physical systems like autonomous robots in manufacturing is becoming increasingly important for automakers as they seek to stay competitive in a rapidly evolving industry.
Cybersecurity Vulnerabilities
Increasingly Complex Systems
CPS are becoming increasingly complex, incorporating cutting-edge technologies such as artificial intelligence, machine learning, and the Internet of Things (IoT). Consequently, this complexity introduces new vulnerabilities and makes them an attractive target for cyber-attacks. Attackers may exploit these vulnerabilities to gain unauthorised access, manipulate system controls, or disrupt the overall operation.
Attack Surface Expansion
The growing interconnectivity of CPS and their increasing reliance on the internet have led to a significant expansion of the attack surface. This means that attackers can exploit not just a single point of entry but multiple interconnected systems, posing a significant risk to CPS integrity.
Physical Risks
Supply Chain Attacks
Supply chain attacks can impact the hardware components of CPS, compromising the security of the entire system. Adversaries may manipulate the components or introduce counterfeit components during the manufacturing process, undermining the system's intended functionality and safety.
Cyber-Physical Security
Cyber-physical security has become increasingly important in the digital transformation age due to the combined process of cyber and physical processes. Fortunately, modern technology can mitigate potential adverse events. Exalens offers a Cyber-Physical Detection and Response AI solution to protect people and companies. It provides Condition-Based Monitoring, Predictive Maintenance, and Network Security Monitoring in one unified platform and automatically analyses and responds to cyber threats, system faults, and equipment failures in seconds for greater operational resilience. By harnessing CPS, this cybersecurity platform can analyse, correlate, and classify cyber-physical data to spot the root cause of threats and provide holistic detection and response.
Conclusion
Cyber-Physical Systems are revolutionising the manufacturing landscape by integrating digital and physical components to create intelligent, adaptive systems. This innovation has led to significant improvements in productivity, flexibility, safety, and sustainability, all while supporting the growing demand for customisation. As the Fourth Industrial Revolution continues to unfold, the increasing adoption of CPS in manufacturing is driving further advancements and is paving the way for a smarter, more connected companies.